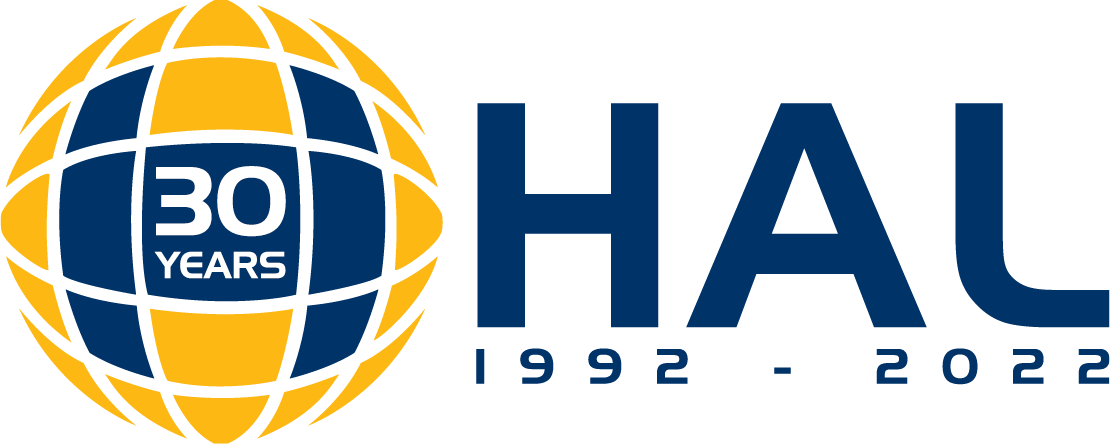
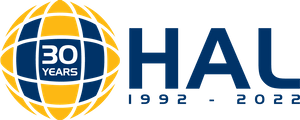
Materials Management Software and Visibility Solutions for Better Supply Chain and
Project Management
Managing Materials from Conception to Consumption
C2C
Contact Us
Please let us know if you have any questions
HAL, Inc.
(281) 260-8181
140 Cypress Station Drive
Suite 131
Houston, TX 77090
© 2019